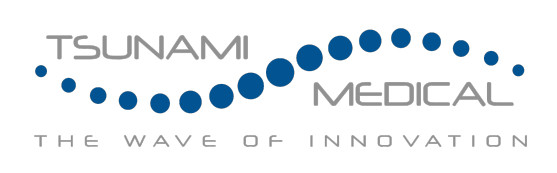
Modena, August 25th 2021 /OrthoSpineNews/
Tsunami Medical, among the leaders in Spine technology innovation focusing on additive manufactured solutions for spine surgery and diagnostic invasive procedures, today announces the launch of 5 of its interbody cage systems made of Tantalum as a base material for its laser-based metal additive technology.
Years of cautious research and dedication by Tsunami Medical’s team have culminated with the achievement of using Tantalum as a safe and reliable alternative for Titanium.
“Tantalum cages show superb micro-elasticity characteristics and therefore meet with the standards of our successfully proven Bone InGrowth Technology®”, said Stefano Caselli, CEO of the company. “Tantalum, is well known because of its excellent biocompatibility and cutting edge Bone InGrowth characteristics, especially from broad experiences in uncemented joint replacement and dental implants.”
Peter Witke, CCO of the company: “Additive manufacturing allows us to resolve issues with previous Tantalum cages, which in the past were manufactured in a traditional way; the unique design characteristics of our Tantalum cages allow a smooth and safe passage along soft tissues and nerve structures.”
Mr. Caselli concludes: “We consider these 3D printed Tantalum cages a meaningful extension of our 3D printed Titanium cage family, and yet another differentiating solution for spinal fusion.” For further information, please feel free to contact our CCO: peter.witke@tsunamimed.com .”
About the Company
Tsunami Medical was founded in 1997, manufacturing invasive diagnostic devices as subcontractor of big manufacturing companies. Over the years the Company has bought the Bloodline trademark, very well known in the international biopsy and vertebroplasty spinal markets.
In 2010 Tsunami Medical started the design and manufacturing of Selective Laser Melting (SLM) technology, resulting in the currently available implant product portfolio.
Located in the heart of the “Biomedical Valley”, nearby Modena (Italy), the manufacturing facility extends on 1200 square meters with modern machinery and clean rooms class ISO 8, 13485 certified to design and manufacture medical devices.